Three steps to recovery the cooling system control when is contaminated.
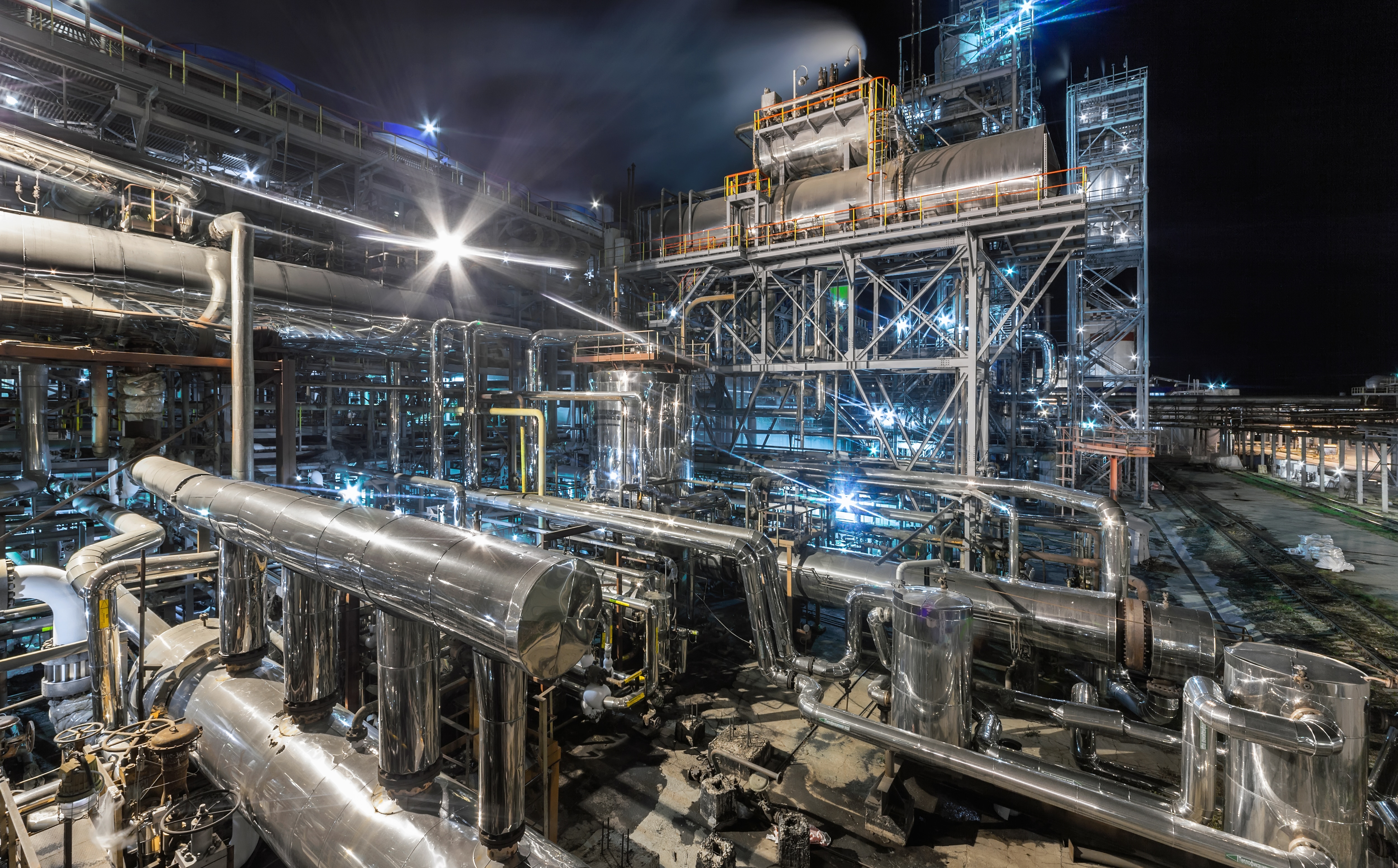
In the chemical and petrochemical industry, contamination with process products in their cooling systems is frequent, affecting their performance and generating high operating costs. Solving it requires timely detection of the leak and correction of the problem, however, this can be a long and limited process, so it is crucial to mitigate its effects and reduce its impact on the performance and operational cost of the Plant.
What are the consequences of process product leaks in the cooling system?
Lack of Microbiological control
The cooling towers provide an excellent environment (temperature, oxygen, light and nutrients) for microorganisms and a process leak into the recirculating water provides additional nutrients such as: hydrocarbons, ammonia, nitrogen, sulfur, etc. which accelerates the proliferation of algae, fungi and bacteria, evidencing problems such as:
• Presence of Biofilm: deposits of microorganism activity, which limit Heat transfer rates
• Microbiological Corrosion (MIC): Several physicochemical mechanisms combine to result in severe and accelerated corrosion.
Presence of Biofilm
Accelerated corrosion by MIC
Fouling:
Process products provide suspended solids and can generate deposits or insulating layers that obstruct or reduce the efficiency of transfer rates.
Corrosion: process contaminations increase the potential corrosiveness of the water and generate deposits that block the action of inhibitors.
How to address contamination with minimal impact on profitability?
Timely action in detecting and correcting the leak will help us to avoid an impact on profitability, however, when mechanical, operational and demand conditions do not allow it, you should use a complete program that includes:
1. Maintenance of a minimum concentration of the contaminant by means of cycle reduction, neutralization, stripping, among others.
2. Reinforcement of the doses of the inhibitor treatment programs.
3. Use of a broad-spectrum biocide program that through an oxidation and disinfection mechanism keeps microorganisms in control. Non-oxidizing biocides are generally an excellent complement to these programs.
Biodetergents can also be used, as they synergistically promote the penetration of the biocide into the biofilm.
In order to maintain microbiological control of contamination with process products with the minimal impact on operating costs, Nalco Water developed the Oxidizing biocide program: ACTIBROM™
How does the Program work?
ACTIBROM™ is a bromine-based product with biodispersant that is blended on-site with a chlorine source (chlorine gas or sodium hypochlorite), generating active bromine with high biocidal power. Depending on the microbiological contamination level, the ratio of chlorine and ACTIBROM in the blend can vary in order to achieve maximum efficiency.
Advantages of the program
Compared to other chlorine-based programs, ACTIBROM requires less oxidant free residual, between 0.1 and 0.2 ppm to achieve biological control, which makes it a more noble treatment for metallurgy.
Table 1. Corrosion rates when replacing with Bromine
Figure 1. Comparative Oxidation Potential to Bromine and Chlorine Metals
This program is widely used in industries with potential ammonia contamination in the cooling water, because when combined with ACTIBROM, bromoamines with a highly effective biocidal power are produced.
Figure 2: Disinfection kinetics at a dose of 1.9 mg/L as Cl2 (2 ppm ammonia)
